A 5 x 12 inch gas-fired surface combustion burner, developed as a corrosion-resistant upgrade of the MR-12 burner to make it more suitable for food processing ovens.
Performance
-
Delivers 20,400 BTU per burner section
-
Develops radiant temperatures up to 1700° F (927° C) at maximum fire with 2.5 to 1 turndown ratio
-
60 sq. in. of burner face per 12” x 5” section, 340 BTU/Sq In
MR-12Ni Exploded:
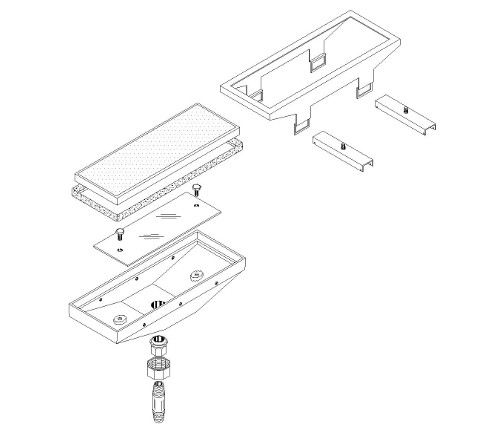
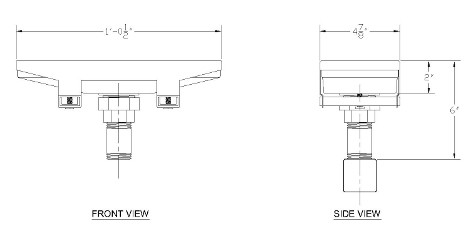
A great benefit of this burner is its relatively high heat flux with low combustion velocity. These attributes along with its flat surface allow it to be placed close to the product yet resist contamination from the volatiles caused by the heating or cooking process. Additionally, the burner achieves an emitter temperature of 1,700° F (927°C) at high fire which prevents the accumulation of bacteria or organic matter. No cooling air plenum is required.
The MR-12Ni has a turndown ratio of 2.5 to 1, allowing it to be operated at a lower temperature (1,100°F) for sensitive products or line slowdown. In the event of a line shutdown, the burner emitters will cool to ambient temperature in a matter of seconds to prevent burning of the product. The burners can then be restarted quickly and reach peak emitter temperatures in seconds. The quick response of the burner results in significant gas savings. Also, labor and lost productivity costs are minimized with shortened heat-up and cool-down periods.
The metal alloy emitter is a fine porosity foam that provides an even combustion surface and enough air/gas flow resistance to reduce the possibility of flashing or burning internally. This emitter is secured in the burner housing by a stainless steel frame and bolts, eliminating the possibility of heat fatigue that can occur with alternative securing systems such as springs or clips.
During assembly of the burner, the edges of the emitter are sealed to prevent debris from shedding from the cut surface. It is also secured in the housing with a high temperature gasket to diminish escape pathways for the air/gas mixture. The emitter is easily replaceable in the event that it is accidentally damaged during routine maintenance or cleaning operations. This replacement procedure is detailed on the back.
The burner maximum capacity is 20,400 btu/hr at high fire and 3.5” W.C. The capacity of the burner will increase at higher air/gas pressures but this is not recommended because it compromises emitter lifetime. The 60 sq in (387 sq cm) of surface area on each 12” x 5” burner section provides an output of 340 btu/sq in (53 btu/sq cm). The radiant output of the burner is approximately 65% IR and 35% convective heat.
The burner is designed to operate best at 19.3 % oxygen in the air/gas feed.