详情
The Protector is ATI Industrial Automation's patented robotic collision sensor designed to prevent costly damage to robotic end-effectors resulting from robot crashes. The Protector's features include: automatic reset, high repeatability, large moment rotation, rugged design and low cost.
The automatic reset feature particularly benefits workplace safety. After the robot crashes, ATI's collision sensor will automatically reset when the robot removes the tooling from the crash-causing object or when torsional rotation does not exceed 20-25 degrees.
Compliant in the X, Y and Z axes, this capability provides a safer method for resetting by making it unnecessary for personnel to enter the robotic work cell.
Along with the Protector’s superior angular compliance, a spring option provides three different breakaway moment settings. This feature provides additional compliance when a low moment trip point is needed. Pneumatic pressure can be added to increase moment capacity for high-inertia motions, and the pressure can be released—relying on the spring alone for low-inertia moves.
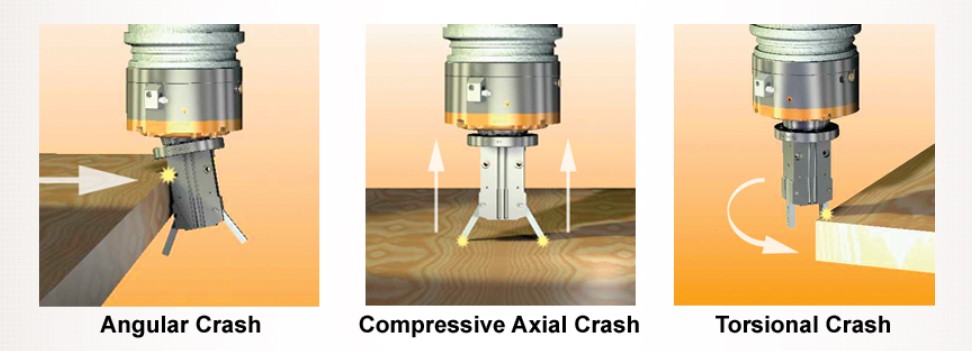
Robotic Collision Sensor Features:
- High Repeatability: Following a collision, the use of precise locating components enables the Protector to reset to within 0.001 inches of its original position.
- Generous Range of Motion: During a crash the Protector can comply large distances in response to any type of crash (angular, axial or torsional) thus allowing the robot controller ample time to take corrective action.
- Rugged Design for Axial Compliance: The rugged design and construction of the Protector, with generous use of hardened tool steel in contact and wear areas, allows the unit to be used as an Axial Compliance Device for end-effectors. The unit can also provide angular and torsional compliance for certain applications.
- Energy Absorption: The impact energy generated during a crash is absorbed by a pneumatic chamber. This protects the tooling from being damaged by crashes. After absorption, this energy is redirected to automatically reset the device upon removal from the crash-causing object.
- Consistent Break-away Response: Break-away response is similar at a given pressure independent of whether the crash is angular, compressive axial, or torsional.
- Flexible Mounting Surfaces: Threaded and through hole mountings are provided for added flexibility. The simple mounting patterns reduce the stack height of the Protector and tooling assembly.
- Automatic Reset: After a crash, the Protector will self-reset when the robot removes the tooling from the crash situation. This eliminates the need to enter the robot cell to reset the crash protection device.
- Optional spring provides two trip points: Air pressure may be used to obtain a higher break-away point during high-inertia motion and the optional preset spring only for a lower break-away point. Inquire about the range of preset springs available for each model.
- Quick-Response Crash Detection: Nuisance tripping of the signal is avoided with the switch set to actuate at 0.020 inches of axial motion. A 3-Pin M8 Connector and cable are used to pass the crash signal.
- Field-rebuildable design (with prior customer training and special tools).
- Field-replaceable connector block assembly.
- IP 65 environmental protection rating (extra cost option).
更多 SK - TEC AUTOMATION & ENGINEERING SDN. BHD. 相关资料