What is Tensile Testing?
Tensile testing, also known as tensile strength testing, is a fundamental materials science test where a sample is subjected to controlled tension until failure. The primary goal of tensile testing is to determine the material’s tensile strength, yield strength, elongation, and reduction in area. This test helps in understanding how materials will behave under various types of forces. Tensile testing is widely used to assess the mechanical properties of materials, ensuring their suitability for specific applications.
Why is this Tensile Testing important?
Tensile testing is crucial for several reasons:
- Material Characterization: Tensile testing provides essential information about the mechanical properties of materials, which is critical for material selection and engineering design.
- Quality Control: Tensile testing ensures materials meet required strength specifications and standards for their intended applications.
- Safety Assurance: Tensile testing verifies that materials can withstand expected loads and stresses, ensuring safety and reliability in products and structures.
- Research and Development: Tensile testing aids in the development of new materials and the improvement of existing ones by understanding their mechanical behavior.
- Compliance with Standards: Tensile testing helps manufacturers comply with industry and governmental regulations.
Concept of the testing (working principle & theory related)
Tensile testing is based on the principles of material deformation and failure under tensile load. The key concepts include:
- Stress and Strain: Stress is the force applied per unit area, while strain is the deformation or elongation per unit length. The relationship between stress and strain helps in understanding the material’s elastic and plastic behavior during tensile testing.
- Elastic Deformation: The initial linear portion of the stress-strain curve, where the material returns to its original shape upon the removal of the load, is observed during tensile testing.
- Plastic Deformation: Beyond the elastic limit, the material deforms permanently during tensile testing.
- Yield Strength: The stress at which a material begins to deform plastically is determined through tensile testing.
- Ultimate Tensile Strength (UTS): The maximum stress a material can withstand before breaking is identified in tensile testing.
- Young’s Modulus: A measure of the stiffness of a material, calculated from the slope of the elastic region of the stress-strain curve, is determined during tensile testing.
These standards provide detailed guidelines on specimen preparation, test procedures, and data analysis to ensure reliable and reproducible results in tensile testing. Compliance with these standards ensures that tensile testing results are consistent and comparable across different laboratories and applications.
Testing Tools
The primary tool for tensile testing is the universal testing machine (UTM), which consists of the following components:
- Load Frame : The structure that holds the test specimen and applies the tensile load during tensile testing.
- Grips : Devices that securely hold the test specimen in place during tensile testing.
- Load Cell : A sensor that measures the applied force during tensile testing.
- Extensometer : A device that measures the elongation or deformation of the specimen during tensile testing.
- Control and Data Acquisition System : Software and hardware that control the test and record data during tensile testing.
How to perform the testing
Performing tensile testing involves several steps:
- Sample Preparation : The material specimen is prepared according to specific dimensions and shapes, often dictated by standards (e.g., dog-bone shaped) for tensile testing.
- Mounting the Specimen : The specimen is placed in the grips of the universal testing machine for tensile testing.
- Setting Up the Test : Parameters such as the rate of loading, initial gauge length, and maximum load are set using the control system for tensile testing.
- Conducting the Test : The machine applies tensile load at a constant rate until the specimen fails. The load and elongation are recorded throughout the tensile testing process.
- Analyzing the Data : The recorded data is used to generate a stress-strain curve, from which various mechanical properties like yield strength, UTS, and elongation at break are determined through tensile testing.
- Reporting Results : The results are compiled into a report that includes the stress-strain curve and calculated material properties from the tensile testing.
Standard for the testing
Tensile testing adheres to numerous international standards to ensure accuracy and consistency. Some key standards include:
- ASTM E8/E8M : Standard Test Methods for Tension Testing of Metallic Materials.
- ISO 6892 : Metallic Materials—Tensile Testing—Part 1: Method of Test at Room Temperature.
- ASTM D638 : Standard Test Method for Tensile Properties of Plastics.
- ISO 527 : Plastics—Determination of Tensile Properties.
- EN 10002 : Metallic Materials—Tensile Testing—Part 1: Method of Test at Ambient Temperature.
These standards provide detailed guidelines on specimen preparation, test procedures, and data analysis to ensure reliable and reproducible results in tensile testing. Compliance with these standards ensures that tensile testing results are consistent and comparable across different laboratories and applications.
Previous testing that have been done
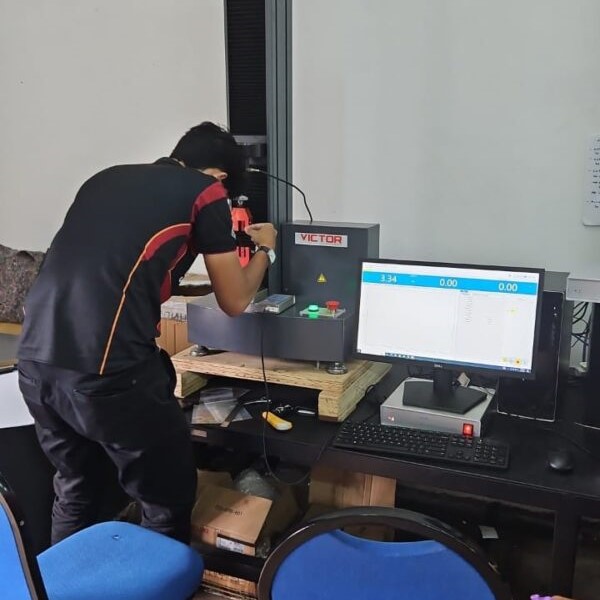