Improved efficiency and reduced slagging and corrosion through SENTROJET chemical injection into coal-fired boiler or furnace
GENERAL
SENTRO TECHNOLOGIES USA, LLC provides a simple, flexible and cost-effective solution to problems arising from the combustion of Coal or Bio-Fuels.
Suggested applications: coal-operated Steam Boilers, Cement Furnaces, or any other coal-operated equipment
Our method is injecting SENTROJET product directly on the coal belt (pre-combustion) or directly into the combustion chamber or the flue gas stream (post-combustion) to produce chemical reactions to oxidize, neutralize and convert residues from combustion which would otherwise increase fouling, corrosion and air pollution.
Reducing fouling, slagging and corrosion will increase the thermal efficiency of the boiler or the furnace, and as a result will reduce fuel consumption, save energy, and reduce pollution.
SENTRO’s cleaning system for heat transfer surfaces and emissions are the result of practical applications combined with continuous research and development.
Example of the problem: Slagging on boiler’s tubes
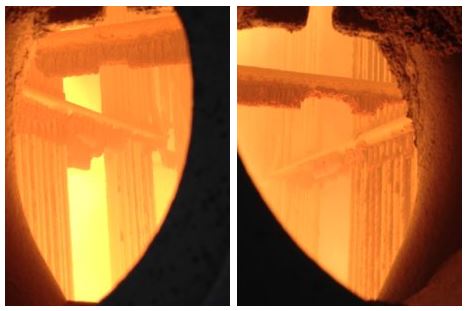
YOUR CHALLENGES
As a result of combustion and depending on the type of fuel and temperatures, vanadium, alkali metal sulfates and alumina silicates will form hard deposits, unburnt carbon and sulfur will form softer and sometimes sticky deposits which will attract other unburnt residue, thereby increasing the thickness of deposits even more. This leads to reduced heat-transfer, blockage of flue gas passages and damage to brickwork.
PROFILE IN LOW TEMPERATURE
Some of the sulfur in the fuel will be oxidized to SO3 which will react with water vapor to form sulfuric acid condensing on surfaces when temperatures are below its dew point. This can also occur when the temperature of the flue gas is above the dew point and the deposits insulate the heat-exchange surfaces. Air-heaters, ducting and stacks are particularly susceptible to this type of corrosion.
PROFILE IN HIGH TEMPERATURE
Vanadium pentoxide with a low melting point will form extremely hard deposits mostly within the super-heater zones. Such deposits are difficult to remove and will give rise to corrosion. Vanadium pentoxide is also a catalyst in the conversion of sulfur dioxide to sulfur trioxide.
Smut, dust and NOx emissions will attract complaints from residents living nearby and these emissions will sometimes exceed limits set by the legislators. The main cause of acidic smutting is unburnt carbon carrying sulfuric acid from the stack. Dust is the particle residue from combustion which escapes from the stack where no or ineffective electrostatic precipitators are installed. The higher the temperature of the combustion, the more NOx is formed. Particularly, the emissions of dust and NOx are subject to tight legislative control.
Slagging inside the boiler
.jpg)
THE SENTRO TECHNOLOGIES SOLUTION
SENTROJET chemical will oxidize unburnt carbon, reduce sulfates and convert vanadium pentoxide to vanadates with a much higher melting point. Deposits will become dry, powdery and disintegrate. They therefore lose their adhesion to heatexchange surfaces.
This complements the air/steam/water soot-blowing, if exist, and increases their efficiency.
SENTROJET chemical will neutralize the sulfur trioxide in the flue gas by the continuous injection of a product containing a water-soluble magnesium compound and which will lower the sulfuric acid dew point temperature to any level required to avoid condensation and therefore corrosion.
Any residue will be dry, powdery and easy to remove. The SENTROJET treatment will also ensure the conversion of vanadium pentoxide to non-corrosive vanadates with such a high melting point that deposits become brittle and flake off. The reaction of SENTROJET with vanadium pentoxide will also inhibit the formation of sulfur trioxide and therefore sulfuric acid.
By oxidizing the carbon deposits, SENTROJET will greatly reduce or eliminate the problem of acid smutting. After oxidation of the unburnt carbon remaining dust particles are less likely to escape into the atmosphere, as their density is greater than that of ordinary soot. The efficiency of separators and electrostatic precipitators will be improved since residues are dry and friable. NOx must be measured accurately and can be reduced by SENTROJET to any level required to satisfy current legislation.
Post-Combustion injection of chemicals directly through the boiler’s wall
.jpg)
Post-Combustion injection of chemicals near the burner
THE SENTRO TECHNOLOGIES TREATMENT IS SIMPLE AND FLEXIBLE
Installation and operation can start at any time without taking the plant out of service and it does not matter whether the plant is in a clean or fouled condition.
The following optional treatment systems are available:
-
Continuous
-
Intermittent but regular (chemical soot-blowing)
-
During start-up and shutdown of plant (24-48 hours)
-
Crash dosing to avoid unscheduled shutdowns and to extend runs
-
Crash dosing to make plant easier to clean
-
Crash dosing to keep plant dry for longer periods during programmed shutdowns
SENTRO TECHNOLOGIES SERVICE
Our technicians will advise the best product, quantity and injection system to meet your requirements. They will supervise the installation and assist your operators with the help of flue gas analyzers and dew point meters to ensure optimum benefit to the customer.
BENEFITS OF SENTROJET TREATMENT
-
Saves energy (less fuel consumption, estimated by 3-10%)
-
Better fuel efficiency without corrosion
-
Reduced cost of soot blowing
-
Greater output and availability of plant
-
Reduced cost of cleaning and maintenance
-
Dry-cleaning instead of water-washing
-
Less damage to brickwork
-
Safer and better working conditions
-
Less pollution
THE ECONOMICS OF SENTRO TECHNOLOGIES
The use of SENTROJET will significantly reduce costs through fuel savings. A SENTRO TECHNOLOGIES representative will assist you in calculating these and other benefits. Estimated fuel saving is 3-10%, depending on: current fuel consumption, burners’ efficiency, overall furnace efficiency, combustion profile, furnace configuration, and other efficiency and structural variables.
SENTROJET SAFETY DATA SHEETS
These are supplied for each product separately and will indicate details of packaging, handling, transportation and storage as required.
Chemicals-Air manifold with flow meters and pressure gauges
Pre-Combustion injection of chemicals on the coal
.jpg)
TECHNICAL ASPECT OF SENTROJET TREATMENT
SENTROJET is the form of an aqueous solution, injected on the coal belt or into the flue path of the boiler or furnace. If post-combustion, injection is done at a point where the flue temperature is greater than 500°C.
Post-combustion injection is done by special lances and nozzles. The driving force for the injection is compressed air at a pressure of 5 to 6kg/cm2. If a compressed air facility is not readily available at the site a pump may be used as an alternative. However it must be assured that the injection pressure is 5 to 6 kg/cm2.
On injection into the hot zone, SENTROJET decomposes and vaporizes. The vapors travel to all parts of the boiler/furnace. It is these vapors of SENTROJET that, by chemical action, loosen and free adhering deposits.
SENTROJET, on decomposition, forms magnesium oxide (MgO), NO2, N2O and Copper II oxide (CuO), and water vapor. The MgO and CuO neutralize low melting point ash deposits by forming corresponding magnesium derivatives. The NO2 and N2O serve to oxidize carbon deposits forming carbon dioxide and elemental nitrogen.
The MgO and CuO also form a grey protective layer on the heat transfer surfaces and this helps in preventing, to some extent, further deposits of unburnt carbon and low melting point ash.
If any sulfuric acid forms due to the sulfur in the fuel the MgO and CuO neutralize this to form magnesium sulfate. SENTROJET treatment, while ramping down for shutdown or ramping up after start up, will significantly reduce the probability of corrosion.
It is during the shutdown and start up processes when there is maximum likelihood of flue temperatures falling below the dew point and, therefore, the greatest risk of corrosion.
If fuel contains vanadium the vanadium gets converted to vanadium pentoxide on combustion. Vanadium pentoxide acts as a catalyst for converting sulfur dioxide to sulfur trioxide. Sulfur trioxide reacts with water vapor to form sulfuric acid.
SENTROJET reacts with vanadium pentoxide to form magnesium vanadate. SENTROJET therefore removes the catalyzing agent that promotes sulfuric acid formation.
In some boilers or furnaces there is the problem of hot spot corrosion. Hot spots are formed when low melting point ash forms a hard insulating layer on the tube surface. Hot spots can lead to tube puncture. SENTROJET treatment removes low melting point ash deposits thus minimizing the possibility of hot spot corrosion.
Two levels of SENTROJET treatment need to be considered:
“clean-up” treatment
“keep clean” treatment
The “clean up” dosage is applicable for treatment of a dirty system.
The requirement of SENTROJET is computed as 0.3 liters of SENTROJET concentrate per ton of fuel consumed over 10 days.
Thus if the clean-up is required of a boiler or furnace system consuming 50 tons per hour of coal, than the quantity of SENTROJET is 50 X 24 X 10 X 0.3 = 3600 liters.
The computed quantity of SENTROJET is to be intermittently injected over a period of time of 10 days.
If only a section of the boiler or furnace is known to be fouled, the dosage of SENTROJET can be logically scaled down. For instance, if it is known that only the fire box of a boiler or furnace is fouled and the heat transfer area in the fire box is 50% of the total heat transfer area of the boiler/furnace the dosage applied can be 50% of the prescribed dosage.
When a boiler or furnace is clean and the aim is to sustain cleanliness the “keep clean” dosage of SENTROJET is applicable.
The monthly requirement of SENTROJET for keep clean is calculated as 0.1 to 0.15 liters of SENTROJET per ton of fuel consumed in a 7 day period.
Thus if a boiler/furnace system consuming 50 tons per hour of coal is to be kept clean, the quantity of SENTROJET required per month would be 50 X 24 X 7 X 0.1 = 840 liters to 50 X 24 X 7 X 0.15 = 1260 liters.
SUPPLEMENTING SENTROJET TREATMENT
On occasion, while SENTROJET treatment may loosen the deposits on heat transfer surfaces, the force of the flue gas may not be adequate to carry these away. In such instances injection of compressed air or high-pressure steam after each injection cycle would be of value.
ADVANTAGES OF SENTROJET TREATMENT
SENTROJET provides the boiler/furnace operator with a number of benefits. These include:
-
The cleaning of the boiler/furnace is carried out On-Line without an unscheduled shutdown.
-
Improved energy efficiency. Stack losses will be reduced.
-
Restoration of lost capacity, in cases where loss of capacity is due to fouled heat transfer surfaces.
-
Reduced corrosion rate.
-
Increased interval between shutdowns, therefore providing greater system availability.
-
Reduction, if not elimination, of soot blowing operations. SENTROJET treatment can be considered a type of chemical soot blowing.
-
Reduced cleaning time when shutdowns are taken.
-
Improved safety since the equipment’s operation is restored to prescribed design parameters.
-
Reduced power consumption of FD and ID fans, since fouling increases pressure drops and therefore fan power requirement.
-
Reduced air pollution since the SENTROJET treatment reduces acid formation and, therefore the possibility of “acid smutting”.
PRICING
(All prices are in $USD and Net of all Fees and Taxes)
Pricing and payment terms to be determined upon additional technical information which is required.