AR Series burners are metal fiber infrared burners with high radiance and all-metal construction. The Apollo-Ray is available in two sizes.
AR-86 Apollo-Ray Burner
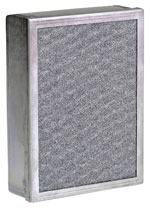
-
8″ x 6″
-
Can be mounted Vertically or Horizontally
-
22,000 BTU/hr/section
AR-125 Apollo-Ray Burner
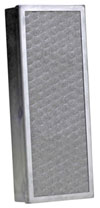
-
12″ x 5″
-
Can be mounted Vertically or Horizontally
-
30,000 BTU/hr/section
UCA-51 Connector Assembly
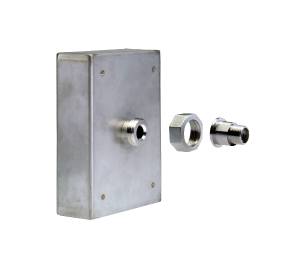
-
Threaded stainless steel 2/3 union connector assembly allows easy removal of each burner from the manifold.
-
Connector assemblies are available in standard 1 ½” or long 2 3/8″
AR-125H – Three manifolds with horizontal burner sections. Three burners mounted on a square tube manifold.
The Apollo-Ray (AR) burner is a surface combustion gas-fired infrared burner. The premixed air and gas passes through the burner body and out through the porous emitter surface. Combustion takes place in a thin layer just above the outer surface.
The Apollo-Ray has a long life due to the sintered metal fiber alloy emitter. Its many micro pores disperse and entrain the air gas mixture. Once ignited, robust infrared radiance is uniformly dispersed over the emitter’s entire surface. This produces fuel savings of 20%+ over knit metal and other fiber burners. The emitter is flexible by nature but backed by a rigid support. This allows it to resist damage during routine maintenance or by thermal shock after repeated firings. When firing face down on a conveyorized product, the emitter remains flat and does not sag, unlike conventional knit metal fiber burners.
The all stainless steel construction of the Apollo-Ray burner body provides excellent heat and chemical resistance. The emitter and its baffle plate are welded to the body. These attributes make the Apollo Ray burner an ideal choice for both industrial and food grade applications. Because it is a flat-faced burner, it can be placed close to the product. Its turn down ratio is a relatively high 2.5 to 1.
Once signaled by the control panel, ignition is easy and flame propagation is fast. Ignition can be provided by a direct spark or a standing pilot. Burners can be monitored by a flame rod or a UV scanner. The burners can be attached to the manifold with standard length (1-1/2”) or long (2-3/8”) union connectors.
The gas inlet can be mounted on the side instead of the bottom producing a low profile burner. A side-mounted low profile burner is only 2-1/8” high, ideal for replacing ribbon burners to achieve higher heating efficiency. Low profile burners are also used between conveyor belts, where space constraints exist.
All Apollo-Ray burners are quick heating and quick cooling. Short heat-up and cool-down periods enhance productivity, save labor costs and prevent excessive heat loads during line stops. The burner sections can be mounted parallel (horizontal) or perpendicular (vertical) to the manifold. This allows the optimal combination of heat flux and length for different applications and line speeds.
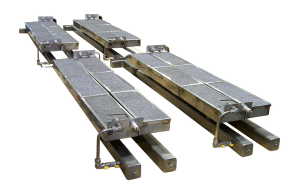