Detection of Insulation Defects in Lithium-Ion Batteries
By measuring the insulation resistance of lithium-ion battery cells before the electrolyte is poured into them, it is possible to detect the presence of metallic foreign matter and damage to the separator at an early stage of the production process.
Target Users
Lithium-ion battery production line technicians
Market Movements
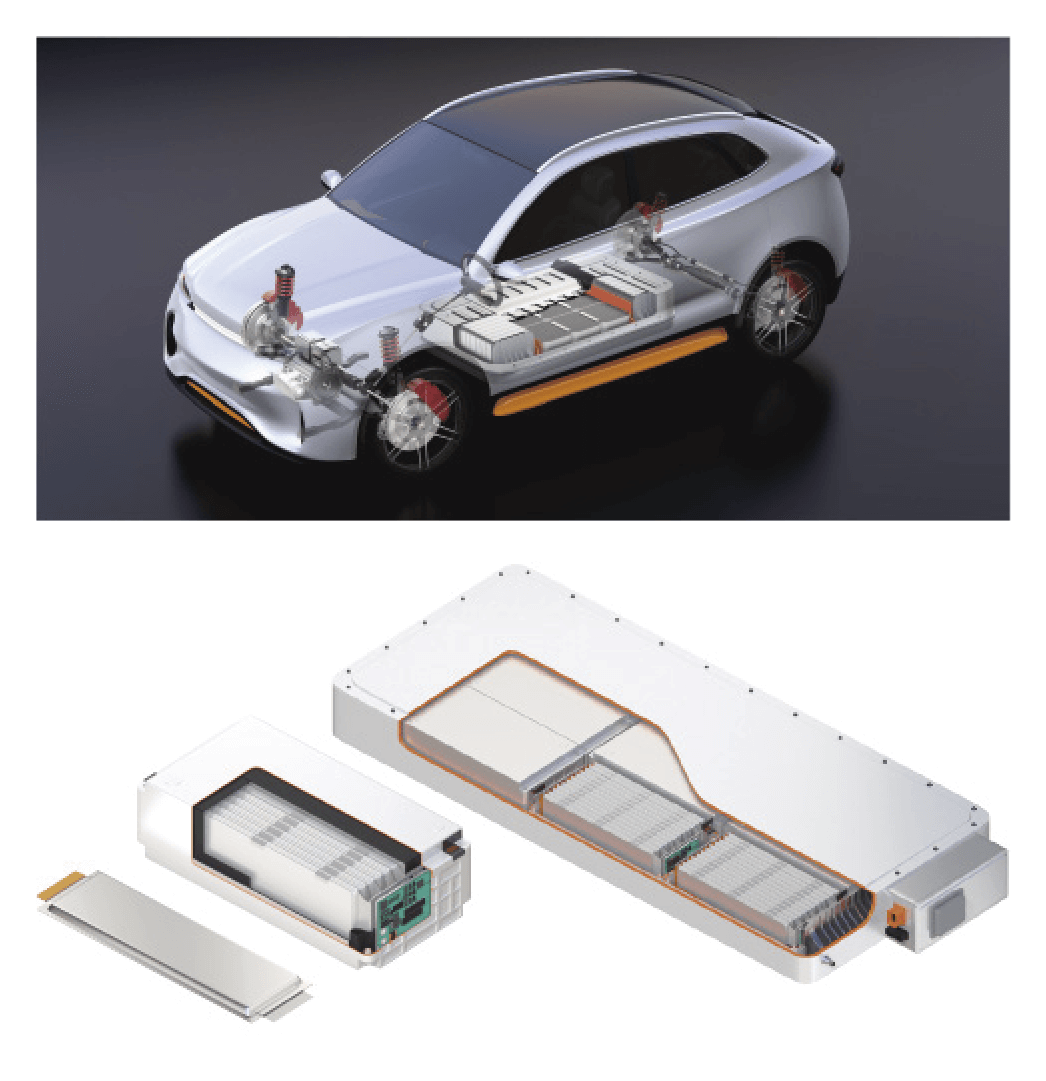
Lithium-ion batteries (LiBs) used in electric vehicles are used for a long period of time in harsh environments. Both of these factors (time and environment) result in quicker degradation of the batteries, which in turn lead to a higher probability of the LiBs igniting in very dangerous fires. Due in part to this, the LiB and automotive markets have been highly focused on improving the safety for LiBs in recent years.
Problem
For LIBs, if there is insufficient insulation resistance, in other words, if the areas that are supposed to be electrically insulated are not properly insulated, it can lead to reduced battery life-span and an increased risk of combustion accidents. The primary causes of bad insulation resistance are metallic foreign contaminants and separator damage.
So, where exactly do these causes of bad insulation come from?
The metallic particulates are slivers of aluminum or copper foil created when the electrode sheets (aluminum or copper foil with chemical composites painted on) are cut into the appropriate size and shape. These fine particulates are often like very fine needles that pierce through the electrode sheet and/or separator, creating a path through which electricity can flow.
The damage to the separators may be anything from a scratch to a cut that occurs during production. Either way, these damages reduce the electric insulation, creating an easier or direct path through which electricity can flow.
Both of these phenomena create paths for electricity where electricity should not flow. When the electricity flows through these paths, it further damages those points. Even worse, and in fact the reason for why these damage are so bad, these currents create heat. This heat, when reaching a certain level, can directly lead to ignition, starting a chain reaction for the whole battery to burn in a fire that is not easily put out. Both of these defects are physically small, so are extremely hard to detect. In addition, with the manufacturing technology of today, they are virtually impossible to prevent. All this translates to the harsh reality of a type of defect that is both prevalent as well as nearly impossible to detect—at least by non-electric means.
Solution
Although these insulation defects are virtually impossible to spot with conventional means, there is one simply way to check for them: to see how electricity actually flows through the battery. By applying a voltage through areas that should be electrically insulated, if the electricity flows too well, one can deduce that these or similar defects exist. This is the insulation resistance test.
Furthermore, from a manufacturer’s perspective, it is essential to find these defects as early in the production process as possible. That way, good parts and labor are not wasted by assembling good parts to faulty parts. The earliest step in which this test can effectively be done is after the cell is assembled but before the electrolyte is poured into it. (As an added note, it is especially important to do this test before adding the electrolyte because applying a voltage in this state damages the battery.)
Testing
So, what does this test look like at the site?
On the production line of a prismatic cell for example, the two electrode sheets are stacked with the separator between them. These three sheets are then rolled up, layer upon layer. Then, the electrode tabs are welded onto the end of each electrode sheet’s end. And finally, it is welded inside a cuboid-shaped enclosure. At this point, the paths through which electricity should and should not flow are in place. Thus, the insulation resistance is ready to be measured.
Check out this page for more details on LiB production and testing.
There are three points at which insulation resistance must be measured: between the two electrodes (before electrolyte filling) and between any point on the enclosure and each of the two electrodes (after electrolyte filling).
This is because these points are effectively the only exterior contact points for the battery: each electrode is a direct path to each electrode sheet, while any point on the enclosure can be considered one point since if electricity flows to one point of the enclosure, it will flow through the whole enclosure.
Our products
Here is a brief overview of products for lithium ion battery insulation testing.
Product model |
BT5525 |
ST5520 |
SM7110 |
SM7120 |
Measurement range |
0.050 MΩ to
9999 MΩ |
0.002 MΩ to
9990 MΩ |
0.001 MΩ to
10000 PΩ |
0.001 MΩ to
20000 PΩ |
Test voltage (DC) |
25 V to 500 V |
25 V to 1000 V |
0.1 V to 1000.0 V |
0.1 V to 2000.0 V |
Basic accuracy |
±1.5% rdg.
±2 dgt. |
± 5% rdg. |
± 0.53% rdg.
±12 dgt. |
± 0.53% rdg.
±12 dgt. |
Measured current |
50 µA to 50 mA |
1.8 mA |
1.8 mA to 50 mA |
1.8 mA to 50 mA |
Dimensions and mass |
Approx. 215 mm (8.46 in) W × 80 mm (3.15 in) H × 306.5 mm (12.07 in) D (excluding protruding parts), Approx. 2.8 kg (98.8 oz) |
215 mm (8.46 in)W × 80 mm (3.15 in)H × 166 mm (6.54 in)D, 1.1 kg (38.8 oz) |
330 mm (12.99 in)W × 80 mm (3.15 in)H × 450 mm (17.72 in)D, 5.9 kg (208.1 oz) |
330 mm (12.99 in)W × 80 mm (3.15 in)H × 450 mm (17.72 in)D, 5.9 kg (208.1 oz) |
Conclusion
In the harsh reality that metallic particulates and damage to the separator cannot be detected by non-electric methods nor completely avoided, testing the insulation resistance is the only solution to counteract the safety hazard posed by these defects. Along with a long list of other products, Hioki provides a vast range solutions for safety testing throughout the battery assembly process.
Related Products List
HIOKI BT5525 Battery Insulation Tester
HIOKI ST5520 Insulation Tester
HIOKI SM7110 Super Megohm Meter
HIOKI SM7120 Super Megohm Meter